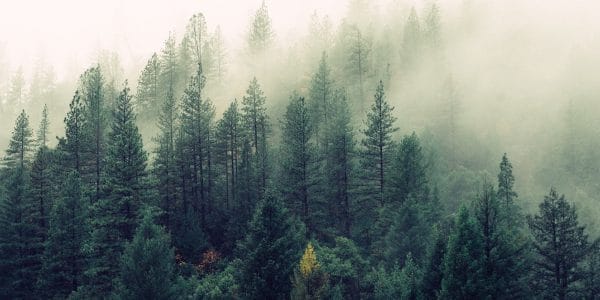
As a manufacturer of laboratory labware, Micronic uses mostly plastic to develop products. By knowing that, we are always looking for ways to reduce, re-use or recycle plastic. In this blog post, we give more information about our vision on waste plastic, what we do with our waste plastic and how we try to contribute to the environment by reducing and recycling our waste plastic. We will explain this according to three questions:
Micronic’s vision on waste plastic
Micronic labware is made by processing raw plastic materials and molding it into tubes, caps or racks. During an injection molding process, it could be possible that waste material is formed, of which most waste is the so called ‘sprues’. Sprues are the pieces of plastic that are left over after the process is finished. This leaves plastic material that cannot be used for our products. What do we do about it? At first Micronic makes great efforts to reduce the total amount of waste plastic. In the future, Micronic even strives to eliminate all sprues after production as these are the largest part of all waste plastic at Micronic. Currently we recycle the waste plastic as much as possible by separating the different materials for recycling.
Different kinds of waste plastic
Micronic uses different plastic raw materials for the production of labware. Examples are: Polypropylene (PP), Polyethylene (PE), Polycarbonate (PC) and Ethyl Vinyl Acetate (EVA). The types of waste plastic at Micronic consist of materials from production: sprues, scrap and residual materials, and besides that plastic bags as a result of the vacuum packing of products in a cleanroom. Micronic tubes, caps and racks are vacuum sealed to make sure no chemicals, residuals, DNA, RNA etc. contaminate the products. Plastic bags that are internally used to transport products within cleanrooms are used multiple times to reduce the use of plastic. All the waste plastic is separated as much as possible for recycling. But what happens after separating the materials?
Recycling waste plastic
Of all waste plastic at Micronic 99% is recycled. Energy is extracted from the 1% that isn’t being recycled (no landfill). The types of waste plastic are stored separately so that they can be processed according to the local recycling program. The PP, PE and PC waste materials are delivered to a local pioneering company in plastic recycling. At Micronic we mostly produce PP products, so the largest part of waste plastic is PP. To make sure that transport for waste plastic is not being overly used, our PP waste material gets compressed making it ultimately 8 times worth the volume than it is without being compressed, reducing the transport.
Environmentally conscious
Micronic takes further responsibility with respect to the environment by its internal environmental management system which is certified by Lloyd’s Register Quality Assurance (ISO 14001). We are committed to comply with and where possible, considerably exceed all applicable laws and regulations related to environmental protection. Next to being ISO 14001 certified, Micronic promotes a more sustainable world with collaborating in the ACT label program from My Green Lab. ACT is the first environmental impact factor label for laboratory products, developed by the non-profit My Green Lab. ACT—which stands for accountability, consistency, and transparency—is designed to provide critical information on the environmental impact of laboratory products.
At Micronic, advancing scientific research to enhance the quality of life is our corporate goal and that extends to our commitment to safeguarding the natural environment for future generations. Read more.